The percentage of sockets checked during an Electrical Installation Condition Report (EICR) greatly varies, primarily influenced by property type, history of electrical maintenance, and the specific environmental risks associated. Normally, 100% testing is mandated for new installations. In comparison, routine inspections typically involve around 25%, escalating to 50% in properties deemed high-risk or during tenancy changes. The choice of sockets for testing adheres to a risk-based approach, focusing on factors such as age, usage frequency, and prior fault reports. Understanding the selection criteria and compliance requirements enhances one’s grasp of the underlying methodologies in electrical safety assessments.
Key Takeaways
- For routine checks, 25% of sockets are typically tested according to industry standards.
- In high-risk areas, testing rates increase to 50% of sockets.
- During a change of tenancy, 50% of sockets are inspected to ensure safety.
- 100% of sockets are tested in new installations to verify full compliance with safety regulations.
- Sampling methods are employed based on risk assessment and property type, ensuring accurate representation.
Table of Contents
What percentage of circuits should be tested in EICr?
In considering the percentage of circuits that should be tested during an Electrical Installation Condition Report (EICR), it is essential to refer to prevailing industry standards which dictate the minimal requirements for safety and compliance.
Factors such as the age of the installation, the environment in which it is located, and the usage patterns of the premises greatly influence the extent of testing needed.
Proper adherence to these guidelines guarantees that the testing is both thorough and effective, safeguarding the integrity of the electrical installation.
Industry standards for socket testing
Stringent industry standards guide the proportion of circuits to be tested during an Electrical Installation Condition Report (EICR). These regulations are designed to guarantee electrical safety, with specific attention to socket durability, the efficacy of testing equipment, and adherence to compliance guidelines.
The standards stipulate a detailed framework for setting inspection frequency based on the environment and usage intensity of electrical installations.
Industry protocols require that a representative number of circuits, including sockets, be tested to assess the overall condition of the electrical system. This typically involves both visual inspections and physical testing using advanced testing equipment.
The criteria for selecting which circuits to test include factors like the age of the installation, previous inspection records, and the type of premises. These inspections are critical in identifying potential faults that could compromise electrical safety.
The percentage of circuits tested must reflect a balance between thorough scrutiny and practical execution, guaranteeing extensive coverage without unnecessary redundancy. This approach not only reinforces the reliability of the electrical installation but also optimises the deployment of resources, maintaining high safety standards while managing the cost-effectiveness of the inspection process.
Factors affecting the percentage checked
Determining the appropriate percentage of circuits to test during an Electrical Installation Condition Report (EICR) involves several vital factors. Key among these are the age and condition of the installation, usage patterns, and environmental influences, which together inform a thorough risk assessment process.
This risk assessment is essential, as it identifies potential electrical hazards and informs the extent of testing necessary to guarantee safety and compliance.
Testing techniques also play a pivotal role. Advanced methods can detect hidden faults more efficiently, thereby influencing the percentage of circuits tested. For instance, thermographic inspections can identify overheating issues not visible to the naked eye, suggesting a more targeted testing approach that might reduce the need to test all circuits in detail.
Furthermore, compliance with established safety standards and regulations must guide the inspection procedures. These standards often specify minimum testing requirements based on the type of installation and its operational environment.
For example, installations in industrial areas might require a higher percentage of testing than those in residential areas due to higher power usage and greater operational risks.
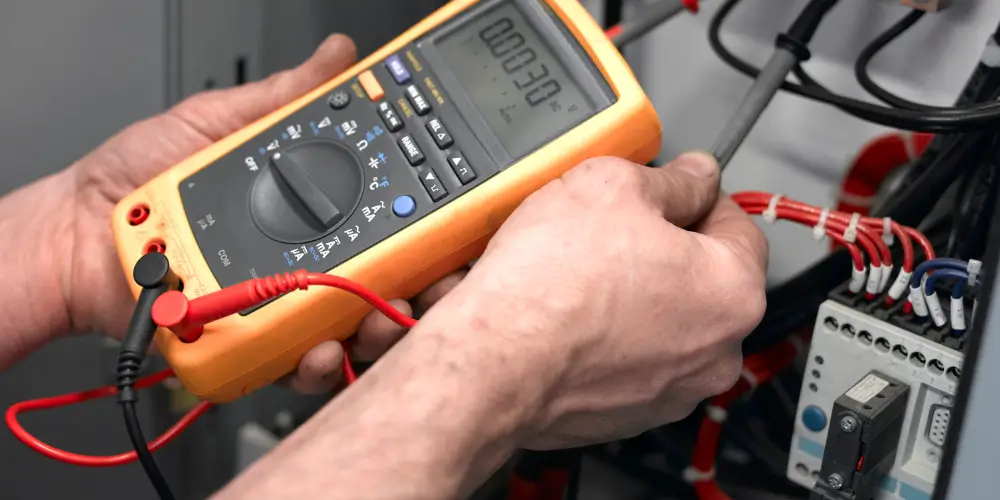
Is Every Socket Tested During an EICR?
During an Electrical Installation Condition Report (EICR), the approach to testing electrical sockets can vary between sampling and conducting a full inspection.
The decision on whether every socket is tested hinges on factors such as the age of the installation, its usage, and any previous maintenance history.
Regulations stipulate that 100% testing may be necessary in environments where electrical safety is critical or where the installation is exposed to high wear and tear.
Sampling vs. full inspection
In the context of an Electrical Installation Condition Report (EICR), not every socket is necessarily tested. The decision between sampling and full inspection hinges on established inspection criteria and risk assessment protocols.
Sampling methods are particularly useful in environments where the quantity of electrical outlets makes full inspection impractical or where preliminary assessments indicate lower risk.
The selection of sockets for testing in a sampling method follows a statistically valid approach, guaranteeing that the sample accurately represents the overall installation’s condition.
This approach, however, requires a deep understanding of the building’s electrical usage, history, and environment to formulate an effective sampling plan. Key factors such as the age of the installation, frequency of use, and environmental conditions influence the risk assessment and guide the sampling strategy.
Testing protocols for EICR are designed to ascertain the safety and reliability of the electrical installation, aligning with strict standards for electrical compliance.
These protocols guarantee that even sampled inspections rigorously test critical aspects of electrical safety, providing a reliable overview without the necessity of testing every single socket.
Through this method, electricians can efficiently identify potential issues while guaranteeing compliance and maintaining high safety standards.
When 100% testing is required
While sampling methods suffice for routine assessments, certain conditions necessitate a 100% testing of all sockets during an Electrical Installation Condition Report (EICR). These situations are guided by full inspection criteria, which include instances of previous poor maintenance, evidence of DIY electrical work, or environments prone to electrical stress and damage. In such cases, a detailed examination is paramount to ascertain the integrity of the electrical installations.
Condition | Inspection Trigger | Required Action |
Prior substandard repairs | Visual evidence of DIY interventions | Full socket testing |
High-risk environments | Locations with moisture, heat, or dust | In-depth analysis |
Reports of frequent faults | Socket failure analysis findings | Test all sockets |
Regulatory compliance | Compliance improvement strategies | Adhere to the latest standards |
Following major renovations | Inspection report essentials updated | Verify new installations |
The testing protocol guidelines guarantee that each socket is tested for correct wiring, resistance, and fault protection to safeguard against potential hazards. This not-incremental approach is vital not only for safety but also for enhancing compliance and operational reliability across the electrical system. Such thorough assessments help pinpoint deficiencies and effectively strategise compliance improvement strategies.
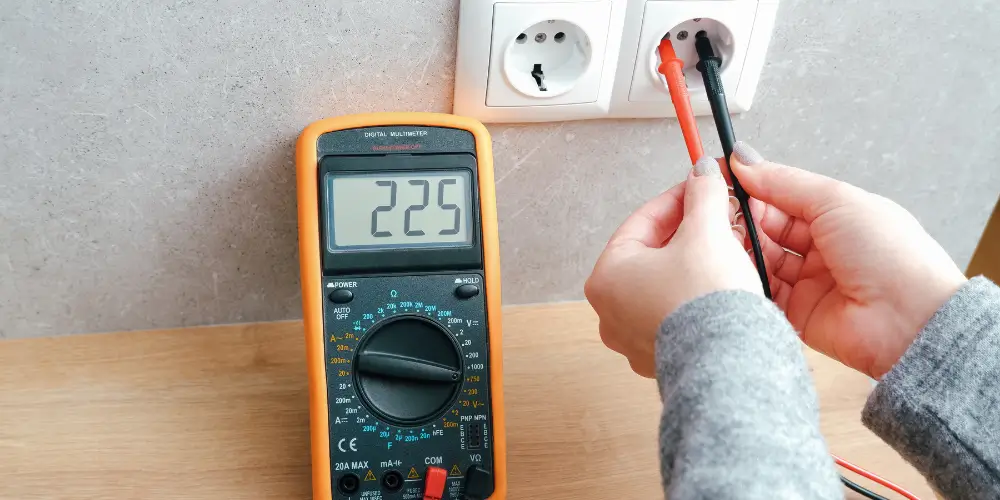
What Percentage of Sockets Must Be Checked?
When evaluating the percentage of sockets that must be checked during an Electrical Installation Condition Report (EICR), the recommended testing rates, which can vary depending on several factors, must be taken into account.
The type of property, whether residential, commercial, or industrial, considerably influences these guidelines, necessitating a tailored approach to each inspection.
Industry standards and regulations typically specify these percentages to guarantee safety and compliance across different settings.
Recommended testing rates
Determining the percentage of sockets that must be inspected during an Electrical Installation Condition Report (EICR) is essential for guaranteeing the safety and compliance of electrical installations.
The recommended testing rates for socket inspection are grounded in both compliance standards and best practices aimed at maximising electrical safety. These standards are not arbitrary but are designed to balance thoroughness with practicality.
To comprehend the depth and rationale behind these rates, consider the following:
- Initial Verification: For new installations, 100% socket testing is mandatory to guarantee that all components meet the regulatory requirements and function correctly.
- Routine Checks: Depending on the environment and usage, at least 25% of sockets should be tested at regular intervals. This helps identify wear and tear or any new issues arising from altered usage patterns.
- High-Risk Areas: In environments with higher electrical load demands or increased operational risks (like workshops or industrial settings), at least 50% of sockets should undergo inspection to preempt safety hazards.
- Change of Tenancy: Whenever there is a change in occupancy in buildings, a thorough inspection of at least 50% of sockets is recommended to guarantee the installation’s integrity for new users.
How property type influences testing
The type of property undergoing an Electrical Installation Condition Report (EICR) greatly affects the percentage of sockets that need to be inspected. Properties vary greatly in relation to age, usage, and environmental exposure, all of which influence the condition and safety of electrical installations.
For older properties, increased scrutiny is necessary due to the likelihood of outdated wiring systems and degraded socket conditions. Such properties often require a higher percentage of socket testing to guarantee compliance with current safety standards.
Conversely, newer properties with recent electrical upgrades might necessitate fewer checks, assuming initial compliance and minimal deterioration.
Tenant occupancy also plays a vital role. High-turnover properties, such as rental apartments, may experience more frequent and varied use of electrical systems, leading to quicker wear and tear. This necessitates a more thorough approach to socket testing to mitigate risks associated with high usage.
Furthermore, regional regulations can dictate the minimum percentage of sockets tested during an EICR. These regulations are often based on local safety codes and historical data pertaining to electrical incidents, guiding inspectors on the requisite scope of examination to guarantee a detailed and effective safety assessment.
Why Are Some Sockets Not Tested in an EICR?
In conducting an Electrical Installation Condition Report (EICR), not all sockets are tested due to various practical constraints.
Factors such as accessibility can impede the extensive testing of every socket; for instance, sockets may be obstructed by heavy furniture or fixed installations.
Additionally, the responsibilities of landlords and homeowners play an important role, as their prior consent and cooperation are essential for the facilitation of thorough inspections.
Accessibility issues and limitations
Accessibility issues and limitations greatly influence why some sockets are not tested during an Electrical Installation Condition Report (EICR). These challenges stem primarily from the physical positioning and environmental factors surrounding the electrical sockets. Understanding these factors is essential for professionals aiming to master the complex norms and standards that govern electrical safety inspections.
Key factors include:
Physical Inaccessibility
Some sockets may be located behind heavy furniture or permanently installed machinery that cannot be moved without significant effort or risk, thereby hindering the inspection process.
Safety Concerns
Testing sockets in areas prone to moisture or other hazardous conditions might pose risks to the inspector. Safety regulations often discourage tests in such environments unless adequate.
Architectural Barriers
Unconventional architectural features can place sockets in difficult-to-reach positions, such as high ceilings, under floors, or behind fixed structures.
Compliance and Procedural
Specific inspection procedures** may limit the testing of sockets that require invasive measures to access, as this could potentially damage.
These accessibility challenges and testing limitations profoundly impact the thoroughness of EICR, demanding adherence to rigorous socket placements and inspection procedures.
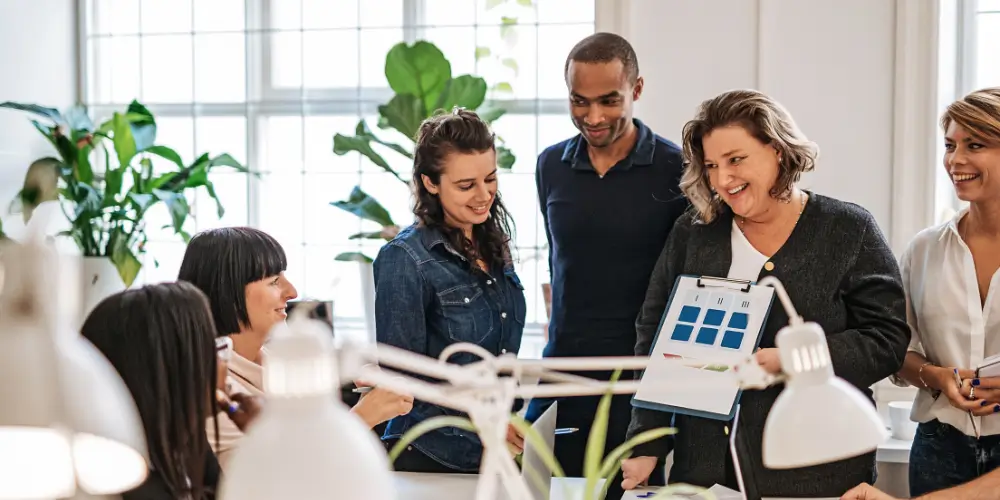
Landlord and homeowner responsibilities
Landlords and homeowners play critical roles in guaranteeing that Electrical Installation Condition Reports (EICR) are as thorough as possible. Yet, there are instances when not all sockets are tested. This partial testing often arises due to the specific landlord obligations and homeowner responsibilities outlined in legal frameworks and safety regulations.
Both parties must guarantee compliance with all legal requirements, maintaining the highest safety standards to prevent electrical hazards.
Landlord obligations include guaranteeing that all accessible electrical systems are inspected and tested by a qualified electrician at regular intervals, as mandated by local housing laws. They must also rectify any identified faults or deficiencies reported in the EICR.
Homeowner responsibilities, particularly for those renting out their property, align closely with those of landlords, requiring them to uphold safety and compliance measures rigorously.
The decision not to test certain sockets can be influenced by various factors, such as accessibility issues, the presence of sensitive equipment, or predetermined agreements based on risk assessments.
Nevertheless, both landlords and homeowners must address any untested sockets promptly, guaranteeing that they do not compromise the overall integrity and safety of the electrical installation.
How Inspectors Decide Which Sockets to Test
Inspectors employ a risk-based selection process to determine which sockets to test during an Electrical Installation Condition Report (EICR).
This method involves evaluating the installation environment, usage patterns, and any visual indicators of wear or damage that suggest potential electrical faults.
Risk-based selection process
When determining which electrical sockets to test during an Electrical Installation Condition Report (EICR), inspectors employ a risk-based selection process that prioritises areas with higher potential safety hazards. This methodical approach is underpinned by robust risk assessment techniques, which guide the inspectors in identifying the sockets that may pose the greatest risk of electrical faults. These techniques are essential in ensuring the safety and compliance of the electrical installation.
A deeper understanding of this process can be appreciated through the following considerations:
- Socket Selection Criteria: Inspectors use criteria such as the age of the installation, usage patterns, and environmental factors to identify high-risk sockets.
- Testing Methodologies Comparison: Various testing methods are evaluated for their efficacy and thoroughness, ensuring the most appropriate ones are applied to identified high-risk areas.
- Inspector Training Importance: Adequately trained inspectors can effectively apply risk assessment models and understand the nuances between different testing methodologies.
- Compliance Implications: Ensuring that risk-based testing aligns with national safety standards is paramount to maintaining regulatory compliance and securing the integrity of the electrical installation.
This structured approach not only enhances the safety of the premises but also optimises resource allocation during EICR assessments.
Signs of potential faults
Often, inspectors are tasked with identifying which electrical sockets to test based on visible signs of potential faults during an Electrical Installation Condition Report (EICR). This selection process is critical to maintaining electrical safety and functionality within residential and commercial buildings.
Inspectors primarily look for fault indicators such as socket wear, which might manifest as physical damage, discolouration, or unusual warmth to the touch. These symptoms suggest internal issues that could precede more severe electrical problems.
Additionally, voltage fluctuations detected through specialised equipment can indicate unstable current delivery, potentially pointing towards compromised wiring or inadequate grounding.
Another critical sign is circuit overload. Inspectors gauge this by examining circuit breaker responses and any historical data on tripped circuits. Frequent overloads can severely impact the electrical system’s integrity, leading to risks of fire or equipment damage.
Wiring deterioration is also a pivotal factor. Signs of ageing, such as brittle, discoloured, or exposed wires or a smell of burning from outlets, are strong indicators of the need for in-depth testing.
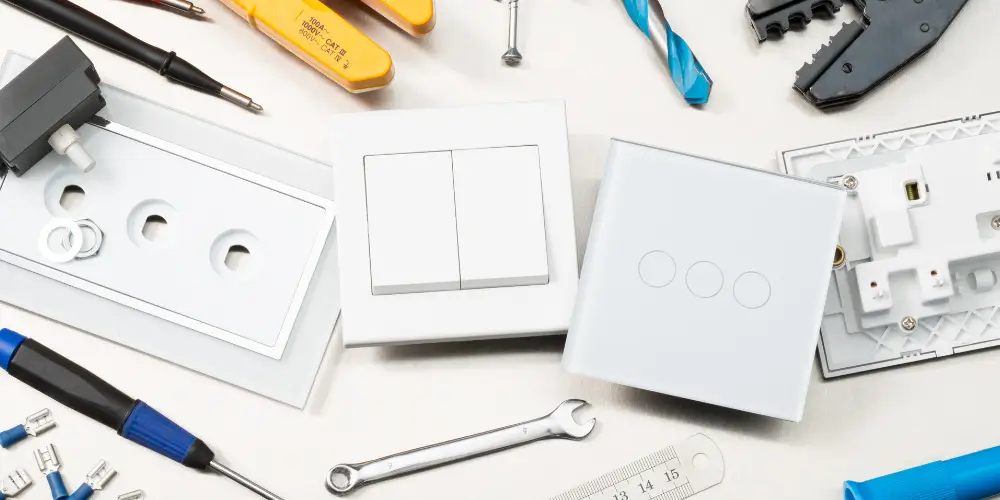
Are Faulty Sockets Always Included in the EICR?
In the Electrical Installation Condition Report (EICR), the inclusion of faulty sockets is determined by their detection during the initial testing phase, which directly impacts the scope of the inspection.
Should defects be identified, the report not only records these faults but also categorises them by severity, which in turn dictates the urgency and nature of subsequent remedial actions.
This systematic approach guarantees that each identified issue is addressed appropriately, enhancing both the safety and compliance of the electrical installation.
How defects impact the testing scope
How do defects influence the extent of testing in an Electrical Installation Condition Report (EICR)? When an electrical defect is identified, the scope of EICR testing often expands to guarantee thorough safety and compliance. This expansion is vital for pinpointing the root cause, evaluating the severity of the issue, and determining the necessary corrective measures.
Here’s how defects specifically impact the testing protocol:
Defect Types Identification
Different defects—be it wear and tear, improper installation, or environmental influences—require varied diagnostic approaches. This necessitates a broader range of testing to identify and categorise the defect types present accurately.
Testing Methods Adaptation
Upon detecting initial defects, the testing methods may need to be adjusted. For instance, a simple visual inspection might escalate to more rigorous testing techniques such as insulation resistance testing or circuit tracing.
Impact Evaluation
The severity and potential risks associated with identified defects guide the extent of further investigations. This impact evaluation is essential for prioritising repair strategies and guaranteeing that resources are appropriately allocated.
Compliance Implications
Defects can have serious compliance implications, influencing the adherence to legal and safety standards. Extensive testing guarantees that all aspects of the installation meet current regulations, thereby avoiding legal repercussions.
Each of these points directly influences the decision-making process regarding repairs and future prevention strategies.
Next steps if issues are found
Discovering faulty sockets during an Electrical Installation Condition Report (EICR) triggers a specific set of follow-up actions to guarantee that all aspects of the electrical installation adhere to safety and regulatory standards.
Initially, the certified inspector will detail each fault in the EICR, categorising them according to their severity—ranging from immediate danger (C1) and potential danger (C2) to improvement recommended (C3). This categorisation is essential as it dictates the urgency and type of repair recommendations.
Following this, the property owner or manager must undertake specific compliance steps. Urgent safety measures are imperative for C1 and C2 classifications. The property manager is responsible for arranging immediate repairs and employing a qualified electrician to rectify the faults swiftly.
Documentation of these repairs is then added to the EICR to reflect compliance with current electrical safety standards.
Furthermore, tenant notifications play a vital role in the process. Tenants must be informed about identified hazards and the steps taken to rectify them, securing their safety and maintaining transparency.
This communication should be clear, detailed, and documented, often forming part of the ongoing property maintenance records. Adhering to these follow-up actions not only guarantees compliance but also enhances the safety and reliability of the electrical installation.
Can You Request a Higher Percentage of Sockets Checked?
In scenarios where the integrity of an electrical installation is critical, clients may request that a greater percentage of electrical sockets be tested during an Electrical Installation Condition Report (EICR).
This heightened level of scrutiny, while contributing to a more thorough assessment, subsequently incurs additional costs due to the increased time and resources required.
Clients should evaluate the necessity of full testing against the potential financial implications.
When full testing is advisable
Full testing of electrical installations, including an extensive check of all sockets, is advisable in situations where the safety and integrity of the electrical system may be compromised by age, visible damage, or alterations.
Professionals must adhere to rigorous testing frequency guidelines to guarantee compliance and safety. Here are key considerations for when full testing is particularly essential:
- Historical Properties: Buildings of significant age are susceptible to the degradation of electrical components. Full inspection scenarios are critical to assess these risks accurately.
- Post-Alteration Verification: Any modifications or extensions to existing electrical systems necessitate thorough electrical safety checks to verify that all changes comply with current standards.
- Visible Wear and Damage: Where there is evident deterioration or damage to the electrical installation, a thorough risk assessment is required. This guarantees that all potential hazards are identified and mitigated.
- Regulatory Compliance: For properties falling under specific regulatory frameworks, meeting compliance documentation requirements involves a detailed examination of the entire electrical system.
These criteria highlight the critical nature of full electrical testing to safeguard property and human life, aligning with established safety and compliance protocols.
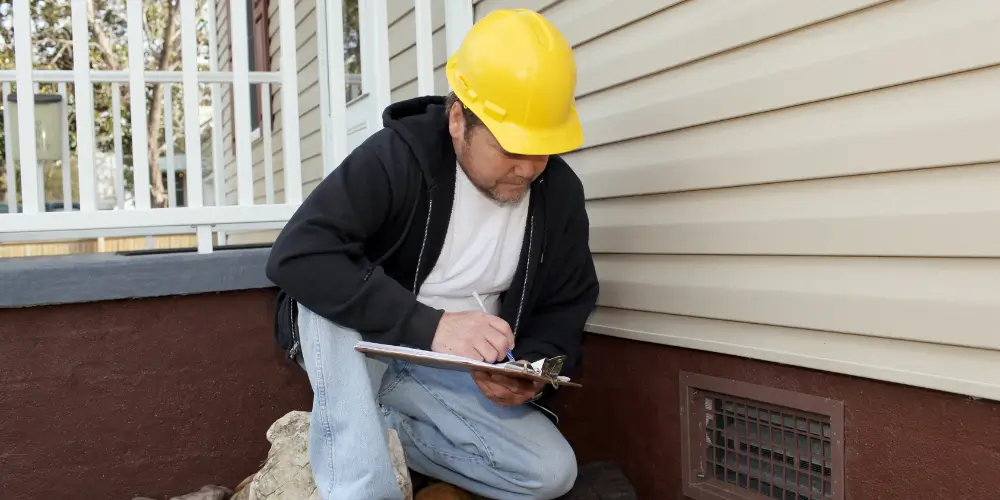
Extra costs for additional inspections
Property owners often consider requesting a higher percentage of socket checks during an Electrical Installation Condition Report (EICR) to enhance safety and compliance assurances. This decision, while prudent, introduces variables such as extra inspection fees, extended inspection duration, and considerations for testing frequency.
Extra inspection fees are typically directly proportional to the extent of the socket checks. The more sockets tested, the longer the inspection takes, so higher charges apply. Qualified inspectors certified to conduct these thorough assessments may command premium rates due to their specialised skills and qualifications. This factor is vital, as the accuracy of the EICR heavily depends on the inspector’s competency.
The duration of the inspection also extends with increased socket testing. This not only affects scheduling but may also necessitate additional visits, further inflating costs.
Property type considerations play a significant role here; larger or older properties with complex wiring systems might require more extensive checks to guarantee a thorough evaluation, consequently escalating the overall expense.
Optimising the balance between thorough safety checks and cost-effectiveness requires careful planning and consultation with experienced professionals. It is advisable to engage a certified inspector to tailor the scope based on specific property needs and compliance requirements.
What Happens If a Tested Socket Fails?
When an Electrical Installation Condition Report (EICR) identifies a failure in a tested socket, several specific faults might be indicated, such as poor wiring connections, damaged socket outlets, or non-compliance with safety standards.
After these issues are detected, qualified electricians must undertake necessary repairs or replacements to bring the installation up to current regulatory standards.
This process guarantees both the safety of the electrical system and its compliance with national electrical codes.
Common faults found
During an Electrical Installation Condition Report (EICR), several common faults may be identified in tested sockets, which can compromise the safety and functionality of the electrical system.
These issues often stem from outdated or improper socket installation practices, inadequate adherence to safety compliance standards, or neglect of maintenance recommendations. Identifying and addressing these faults is vital for ensuring the electrical system operates safely and efficiently.
Here are four common faults typically found during an EICR:
- Overloaded Circuits: Sockets may fail due to excessive electrical load capacity being demanded from them. This is often a result of inadequate planning in relation to the number and type of appliances being powered from a single socket.
- Poor Wiring Connections: Common wiring issues include loose, corroded, or improperly secured wiring. Such conditions can lead to arcing, overheating, and potentially fire hazards.
- Damaged Outlets: Physical damage to the sockets, often from wear and tear or forceful use, can expose wiring or create contact issues that disrupt power flow and pose safety risks.
- Non-compliance with Standards: Sockets not installed according to the latest safety compliance standards are more prone to failure. This includes the absence of necessary safeguards such as ground fault circuit interrupters (GFCIs).
Maintaining vigilance in these areas is essential for upholding the integrity and safety of an electrical installation.
Repairs and compliance steps
Should a socket fail during an Electrical Installation Condition Report (EICR), immediate remedial action is required to restore both compliance and safety standards.
The initial step involves a detailed diagnostic procedure using advanced testing equipment to ascertain the specific cause of failure, which could range from wiring deterioration to faulty socket design.
Upon identifying the root issue, specialised repair techniques are employed. These may include re-wiring, replacing defective components, or upgrading the entire socket system to meet current compliance regulations.
The repair work must adhere strictly to the latest safety standards, ensuring that no further hazards arise from the socket’s use.
Post-repair, the socket must undergo a rigorous series of tests as per standardised inspection protocols. This is to verify that the repairs have effectively corrected the fault and that the socket now complies with all regulatory requirements.
Documentation of the repair process and test results is essential for future inspections and for maintaining a record of compliance.
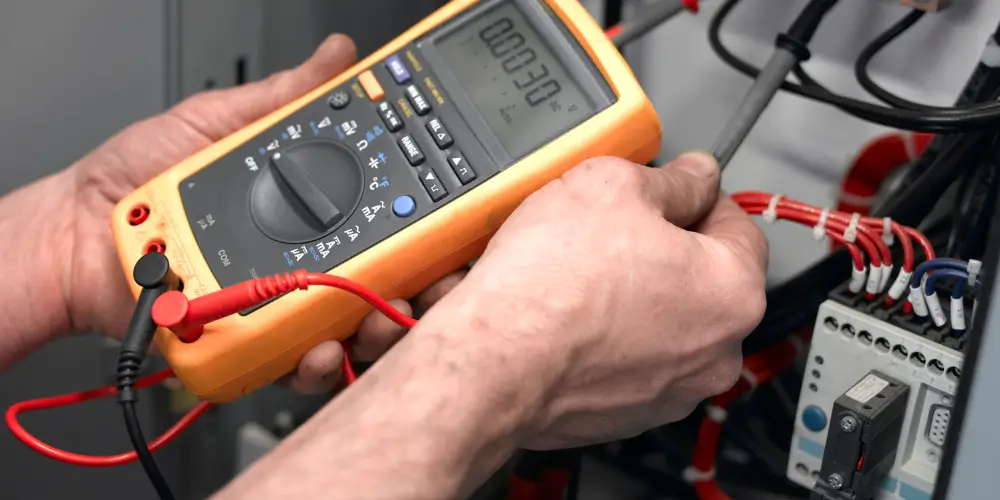
How Often Should Sockets Be Tested?
The frequency of socket testing varies considerably between residential homes and commercial businesses, reflecting the differing levels of usage and potential risk.
Stringent regulations mandate regular inspections for rental properties, often aligned with tenancy changeovers or, at minimum, every five years to guarantee compliance with safety standards.
Property owners and managers need to adhere to these guidelines to maintain electrical safety and prevent potential hazards.
Frequency for homes and businesses
Determining the appropriate frequency for testing electrical sockets in homes and businesses is essential for guaranteeing safety and compliance with national standards.
Establishing a regular inspection schedule is not only a matter of safety but also a proactive measure to maintain electrical compliance and optimise socket safety. The testing frequency should take into account various factors, including the age of the electrical installation, the type of premises, and the intensity of use.
Here are specific guidelines to take into account for setting the appropriate testing intervals:
Residential Properties
Typically, socket testing is recommended at least every 5 years or during any major renovation. This interval guarantees that any potential deterioration or damage can be identified and rectified in a timely manner.
Commercial Establishments
For businesses where the usage of electrical sockets is generally higher, testing should be more frequent, approximately every 5 years. This helps maintain a safe working environment and uphold electrical compliance.
Industrial Facilities
Given the high demands and heavy machinery, industrial settings should have their sockets tested at least every 3 years.
Following Significant Alterations
Whenever there are significant changes or additions to the electrical system, a thorough inspection should be conducted to assess.
These intervals align with the principles of risk assessment and guarantee the longevity and safety of electrical systems, reflecting the key inspection benefits.
Regulations for rental properties
For rental properties, the regulations stipulate that electrical socket testing must be conducted at least every five years. This requirement is part of a broader set of standards aimed at guaranteeing tenant safety and electrical compliance within the residential rental sector.
Property management teams and landlords are obligated to adhere to these regulations to maintain the certification and legal operation of their rental units.
The five-year interval for socket testing is established to detect potential degradation or faults that could pose risks to occupants. These inspections are part of a thorough Electrical Installation Condition Report (EICR), which a qualified electrician must carry out.
The EICR assesses the safety of electrical installations, including sockets, to prevent electrical hazards that could lead to fires or electrocution.
Landlord obligations extend beyond simple compliance; they must guarantee that all electrical installations are not only operational but also safe for continuous use.
Failure to comply with these standards can result in legal repercussions and jeopardise the safety of tenants.
Therefore, regular rental inspections serve as a critical mechanism for upholding these standards, reinforcing property management’s commitment to tenant safety and regulatory adherence.
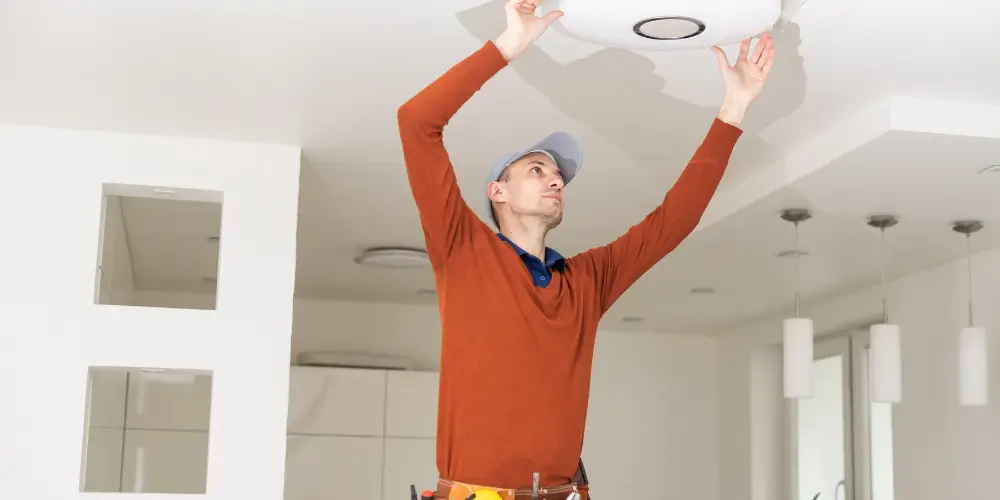
How to Ensure Your Property Passes the EICR
Initiating an exhaustive pre-inspection checklist is essential to guaranteeing your property successfully passes the Electrical Installation Condition Report (EICR).
This checklist should include a detailed review of all electrical systems, with a particular focus on identifying and upgrading any outdated or deteriorating wiring.
Pre-inspection checklist
A meticulous pre-inspection checklist is essential for ensuring that your property successfully passes the Electrical Installation Condition Report (EICR). This preparation is essential not only for compliance but also for the safety and reliability of your property’s electrical system.
The following steps guide property owners through important inspection preparation, emphasising the checklist importance for a successful EICR evaluation:
- Review Current Electrical Compliance Standards: Familiarise yourself with the latest electrical safety regulations to confirm that your property’s electrical system meets legal requirements. This knowledge will guide your preparation and highlight potential areas of concern.
- Document the Installation: Compile detailed records of your electrical system, including circuit diagrams and modifications. This documentation aids in the quick identification of issues and guarantees a thorough assessment.
- Check Socket Safety: Examine all sockets for signs of damage, overheating, or faulty installation. Making certain that all sockets are safe and functional is a vital component of the pre-inspection guidelines.
- Test Safety Devices: Verify that all residual-current devices (RCDs) and circuit breakers are operational. These devices are essential for preventing electrical shocks and fires, contributing notably to overall electrical safety.
This strategic approach not only prepares your property for inspection but also enhances its electrical safety and functionality.
Upgrading outdated wiring
Addressing the issue of outdated wiring is a critical step in guaranteeing that your property meets the standards required for a successful Electrical Installation Condition Report (EICR). Modernising electrical systems not only brings them up to current compliance requirements but also enhances overall safety and functionality. Outdated wiring solutions typically involve replacing old, non-compliant cabling and devices with materials that adhere to the latest electrical codes.
While costly, the process offers significant benefits. Upgrades can prevent potential hazards such as electrical fires and reduce the risk of equipment failure due to inadequate power supply. The increased efficiency and safety of the electrical installation generally offset the long-term cost implications of upgrading.
To illustrate the importance of these upgrades, consider the following table:
Aspect | Details |
Safety Improvements | Reduces risks of electrical fires and shocks. |
Compliance Requirements | Guarantees wiring meets current national standards. |
Benefits of Upgrades | Enhances property value and guarantees reliability of electrical supply. |
Upgrading outdated wiring is imperative for property owners aiming to pass the EICR. It’s a proactive measure that safeguards residents and investments alike.
Frequently Asked Questions
What Are the Consequences of Not Testing Enough Sockets?
Not testing enough sockets can lead to severe electrical hazards, undermining socket safety. This negligence may result in compliance issues, affect the validity of property insurance, and infringe on tenant rights, jeopardising overall safety and legal standing.
Who Is Qualified to Perform an EICR?
Only professionals with EICR certification, demonstrating advanced qualified electrician skills, can legally conduct EICR. This process underscores the importance of the EICR report, adheres to legal requirements, and aligns with the recommended EICR frequency to guarantee electrical safety compliance.
What Tools Are Used During Socket Testing?
During socket testing, professionals use testing equipment like insulation resistance testers and socket testers to guarantee electrical safety and compliance with standards. Regular maintenance frequency enhances reliability and adheres to prescribed safety protocols.
How Long Does an EICR Socket Test Typically Take?
The duration of an EICR socket test varies based on testing frequency and inspection efficiency. Typically, it ranges from several minutes to hours, ensuring thorough electrical safety assessments through detailed socket testing procedures.
Are There Different Requirements for Commercial Versus Residential Properties?
Yes, commercial standards are more stringent than residential standards, reflecting regulatory differences that prioritise safety implications. Commercial properties often require more frequent testing to guarantee compliance, underscoring the higher risks associated with their electrical systems.