Ensuring Safety, Empowering Trust
Secure your peace of mind with a London Safety Certificate. Serving North London, we offer expert PAT testing with precision and efficiency. Connect with us today to ensure your electrical safety!
ONLY £49.99
* All inclusive (No hidden Cost)
* Limited time offer upto 2 weeks from now
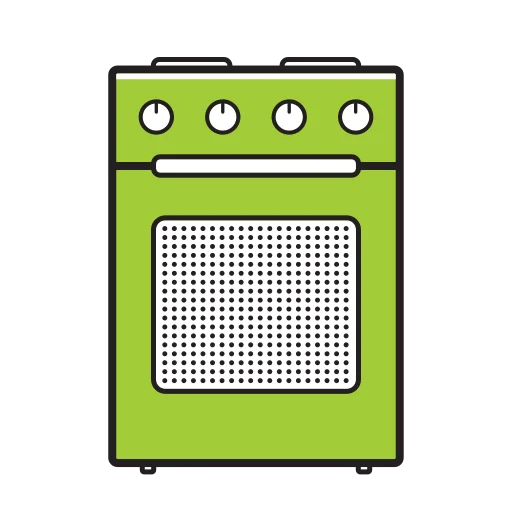
London Safety Certificate – Premier PAT Testing Services in North London
In North London, Portable Appliance Testing (PAT) is a critical procedure designed to ensure that electrical appliances meet stringent safety standards, thus safeguarding against potential hazards in the workplace. Governed by the Electricity at Work Regulations 1989, PAT encompasses a comprehensive examination, from initial visual checks to in-depth electrical testing, confirming the functionality and integrity of each appliance. Regular PAT is mandated to comply with health and safety legislation and maintain operational efficiency and employee safety. Certified professionals employing advanced diagnostic tools carry out these tests, providing the necessary certification to demonstrate compliance. A deeper exploration into regular PAT services offered in North London will benefit businesses aiming to enhance their safety protocols.
London Safety Certificate offers top-tier PAT Testing services across North London, catering to various clients, from small businesses to large enterprises. With over a decade of expertise, the company utilises state-of-the-art equipment to ensure that all portable appliances are thoroughly inspected and tested for safety and compliance. Recognised for their reliability and efficiency, they provide emergency testing services to meet urgent needs without sacrificing quality. London Safety Certificate is renowned for its competitive pricing and transparency, ensuring no hidden costs. It has consistently earned high praise and five-star reviews from satisfied customers, underscoring its commitment to excellence in electrical safety.
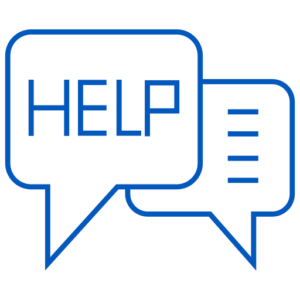
HOW CAN WE HELP
At London Safety Certificate, we specialise in providing top-tier Portable Appliance Testing (PAT) services across North London, ensuring that businesses comply with safety regulations and standards. Our team is committed to delivering reliable, efficient, and thorough PAT testing solutions tailored to meet each client’s unique needs. By choosing our services, customers can rest assured that their electrical appliances are rigorously inspected and certified, minimising the risk of electrical hazards and enhancing workplace safety. Trust us to uphold the integrity of your operational standards with our expert PAT testing services, fostering a safer environment for all.
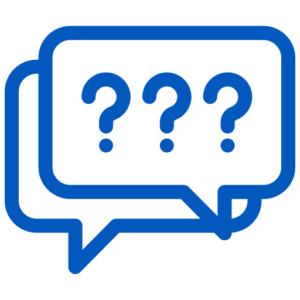
WHY US
At London Safety Certificate, we pride ourselves on providing top-tier PAT Testing services tailored to the diverse requirements of North London’s commercial and residential spaces. With over a decade of specialised experience, our team leverages state-of-the-art testing equipment to ensure maximum safety and compliance with electrical standards. Our commitment to reliability, efficiency, and thoroughness has earned us a high customer retention rate and consistent 5-star reviews. Opting for our services means benefiting from competitive pricing, no hidden fees, and the availability of emergency testing services without compromising on quality. Choose the London Safety Certificate for dependable electrical safety solutions that you can trust.
What is PAT Testing, and why is it Essential?
Portable Appliance Testing (PAT) is a critical procedure for inspecting electrical appliances to ensure their safety. This process significantly reduces the risk of electrical accidents and is essential for maintaining electrical safety and workplace compliance with health and safety regulations.
PAT testing is pivotal in business risk management strategies, as it systematically identifies defective electrical equipment before it can cause harm.
The importance of PAT testing extends beyond mere compliance. It is integral to fostering a safety culture within organisations, emphasising the well-being of employees and the operational integrity of business processes.
Regular testing and certification of appliances extend the equipment’s lifespan, preventing premature disposal and replacement costs. Moreover, insurance requirements often mandate rigorous electrical safety protocols, including PAT, to minimise claims related to electrical faults.
Technician qualifications are paramount in PAT testing, as the testing accuracy depends heavily on the professionals’ expertise. Certified technicians equipped with specialised knowledge and tools are better positioned to detect anomalies in electrical appliances that might be overlooked otherwise.
Incorporating PAT testing into routine maintenance schedules can lead to significant cost savings for organisations. By identifying faulty appliances early, businesses can avoid the higher costs associated with equipment failure, including productivity losses and more severe reparative measures.
Ultimately, PAT testing is not just about compliance or meeting insurance standards—it’s about integrating a proactive safety and risk management approach that prioritises reliability and efficiency across all operational facets.
Book NowBenefits of Regular PAT Testing
Understanding and adhering to the legal framework for PAT testing is foundational for workplace safety. Beyond regulatory compliance, regular Portable Appliance Testing (PAT) brings many operational advantages that businesses should pay attention to.
Firstly, PAT contributes significantly to cost savings. By identifying malfunctioning or suboptimal equipment early, businesses can avoid the higher costs associated with unexpected equipment failures and downtime. This proactive maintenance helps extend the equipment’s lifespan, ensuring that capital investments yield maximum returns over a longer period.
Moreover, regular PAT plays a crucial role in risk reduction. It minimises the likelihood of workplace accidents caused by defective electrical equipment, thereby enhancing employee safety. This protects staff and reduces the potential legal liabilities and costs associated with workplace injuries.
Insurance benefits are another critical aspect. Many insurers offer reduced premiums to businesses that adhere to rigorous safety standards, including regular PAT. This can be seen as acknowledging the insured entity’s decreased risk profile.
Furthermore, consistent PAT testing bolsters workplace morale by reinforcing management’s commitment to safety. This can lead to increased productivity as employees feel more secure and valued.
Regular testing facilitates effective asset management by systematically tracking the condition and performance of electrical assets. This practice also strengthens compliance confidence, ensuring that businesses meet safety standards consistently.
Lastly, regular PAT enhances customer trust by demonstrating a commitment to safety and reliability. It also promotes energy efficiency by ensuring all equipment operates optimally, reducing unnecessary energy consumption.
Legal Requirements for PAT Testing
In the United Kingdom, the legal requirements for Portable Appliance Testing (PAT) are primarily governed by various health and safety legislation. These regulations are designed to ensure that all electrical appliances in workplaces are safe for use, thereby reducing the risk of accidents and maintaining compliance standards.
The legal framework is based on the Electricity at Work Regulations 1989, which impose a duty on employers to take practical steps to ensure that electrical appliances are not dangerous. This requires implementing a regular maintenance, inspection, and testing program.
To understand the depth of these legal obligations, consider the following key points:
Adherence to these safety regulations and legal standards is not merely about fulfilling legal obligations; it ensures workplace safety and minimises liability risk. Conducting a thorough PAT by a certified professional helps maintain equipment safety and supports a culture of safety first in the workplace. Hence, understanding and applying these regulations is crucial for all business stakeholders in North London and beyond.
Benefits of Certified PAT Testing in London
By obtaining certification in PAT Testing London, you enhance your credibility and demonstrate proficiency in ensuring electrical appliance safety. Certified PAT testing offers cost-effective solutions by identifying potential issues early, preventing costly breakdowns, and ensuring equipment reliability.
Adhering to industry standards, certified testing procedures guarantee that your appliances meet safety requirements, reducing the risk of accidents. In addition, by investing in certified PAT testing in London, you enhance customer satisfaction as they trust in the safety and reliability of your electrical equipment.
Certified testing not only fulfils legal obligations but also boosts the overall safety of your workplace, preventing fire hazards and potential injuries. Ultimately, choosing certified PAT Testing in London provides peace of mind, knowing that your appliances are safe, compliant, and operating efficiently, which is essential for a secure and productive working environment.
Book nowIdentifying Equipment for PAT Testing
Identifying which electrical appliances require portable appliance testing (PAT) is a critical initial step to ensure comprehensive safety and compliance within the workplace. This process involves meticulously assessing all electrical equipment to ascertain its suitability for PAT and the specific requirements dictated by its operational environment and associated risks.
The classification of equipment types is pivotal for delineating the scope of testing. Various electrical appliance classes— from handheld devices to large stationary machines—necessitate distinct approaches in testing standards and inspection intervals. For instance, equipment frequently moved or subjected to harsh operational conditions may require more frequent assessments than stationary or less frequently used appliances.
Adhering to safety guidelines is non-negotiable when identifying equipment for PAT. These guidelines ensure that the selected appliances for testing align with the latest health and safety regulations, thus mitigating the risk of electrical hazards. Moreover, compliance audits periodically verify that these safety standards are consistently met across all tested appliances.
Technician qualifications play a crucial role in this phase. Only certified professionals with a deep understanding of risk assessment, electrical standards, and testing protocols should conduct the identification and subsequent testing phases. This ensures accuracy in:
Understanding these elements is fundamental to maintaining optimal workplace safety and ensuring compliance with electrical safety norms.
Book NowThe PAT Testing Process
Once the equipment for Portable Appliance Testing (PAT) has been identified and classified, the next crucial step is the testing process. This phase demands high precision and adherence to established safety standards to minimise electrical hazards. Each piece of equipment undergoes rigorous testing techniques to detect operational shortcomings or safety risks.
Technician training is fundamental in this phase. Technicians must have a profound understanding of various electrical systems and their potential risks. This knowledge ensures they can perform risk assessments effectively before proceeding with the testing.
Equipment calibration is another critical aspect; it guarantees that all testing devices provide accurate readings, essential for reliable results.
The testing process involves several key procedures, including visual inspections to identify any obvious damage or defects, functionality tests to ensure that equipment operates correctly, and electrical tests to assess the integrity of the equipment’s electrical components.
Inspection intervals are strictly adhered to, ensuring that each piece of equipment is tested appropriately to maintain safety and compliance.
Documentation practices are meticulously followed throughout the process. All findings, from initial risk assessments to final test results, are systematically recorded. This helps maintain records for compliance purposes but also aids in troubleshooting procedures if issues are later identified.
Emergency protocols are also an integral part of the testing process. Technicians are trained to handle and mitigate unexpected situations effectively, ensuring the testing environment remains safe.
This comprehensive approach to PAT testing ensures that all equipment in North London meets the required safety standards.
Book nowHow often does PAT Testing need to be carried out in North London?
Determining the appropriate frequency for Portable Appliance Testing (PAT) in North London requires a nuanced understanding of regulatory standards and specific operational conditions.
Factors such as the type of equipment, its usage, the environment, and the potential risks associated with electrical hazards significantly influence PAT testing frequency.
More frequent testing is crucial for environments with high equipment usage or where safety is paramount, such as construction sites or medical facilities. The Health and Safety Executive (HSE) suggests that these environments may require PAT every three to six months to mitigate risks effectively.
Conversely, less hazardous environments, such as office settings, where equipment undergoes mild usage, might extend the testing intervals annually.
Compliance guidelines dictate that all service providers conducting PAT must adhere strictly to the codes of practice laid out by relevant authorities. This ensures the longevity and functionality of the electrical appliances and safeguards against potential electrical hazards that could lead to injuries or fatalities.
Risk assessment plays a pivotal role in determining the testing intervals. A thorough assessment should consider factors like equipment lifespan, maintenance schedules, and operational demands specific to North London’s industry specifics.
It’s advisable to consult with certified professionals who can tailor the PAT frequency to your specific needs, ensuring both compliance and safety.
Frequency of PAT Testing
Portable Appliance Testing (PAT) frequency is determined by several factors, including the type of equipment, its use, and the environment in which it operates. Understanding these variables is crucial to aligning with industry guidelines and ensuring electrical safety and workplace compliance. Each equipment category will have different requirements for PAT testing frequency, influenced by its susceptibility to wear and the risks associated with its failure
Equipment Usage and Handling
Frequent use of equipment subjected to rough handling necessitates shorter testing intervals. This is crucial for equipment in construction or manufacturing settings where rough use is common.
Environment
Equipment used in harsh environments, such as high humidity, dust, or temperature extremes, requires more frequent checks. Such conditions can accelerate wear and increase electrical safety risks.
Type of Equipment
Stationary, IT, and portable appliances each have specific risks and maintenance needs that affect the testing frequency. For instance, portable heating appliances need more frequent scrutiny than stationary desktop computers.
PAT testing frequency must be strategically planned and incorporated into the broader maintenance schedules to optimise equipment lifespan and uphold safety standards. A thorough risk assessment should guide the scheduling of PAT tests, ensuring that all potential hazards are mitigated effectively.
Common PAT Testing Myths
While Portable Appliance Testing (PAT) is essential for ensuring electrical safety, several myths persist that need clarification and lead to unnecessary concerns or complacency.
Perpetrating these myths undermines the effectiveness of safety protocols, potentially leading to non-compliance with industry regulations and inadequate risk assessment practices.
Myth 1: PAT testing is prohibitively expensive. Contrary to common belief, the cost of PAT testing is moderate and should be viewed as a prudent investment in safety. The expenses of non-compliance and potential accidents far outweigh the cost of regular testing.
Myth 2: Only older appliances need testing. This misconception can lead to serious safety oversights. All electrical equipment, regardless of age, can become faulty. Regular testing ensures that new and old appliances adhere to stringent equipment standards and maintenance practices.
Myth 3: PAT testing causes unnecessary downtime. Efficient planning and using qualified technicians can minimise any disruption to operations. Testing can often be scheduled during off-hours, ensuring minimal impact on productivity.
The focus on debunking these myths is crucial for fostering a culture of safety and compliance. Enhanced understanding combats testing misconceptions and supports the implementation of robust maintenance practices.
Moreover, employing technicians with proper qualifications ensures adherence to equipment standards and industry regulations.
Effective PAT testing is not just about compliance—it is a fundamental component of a comprehensive risk management strategy, safeguarding personnel and equipment.
Book nowPreparing for a PAT Test
Understanding the importance of PAT Testing Certification, it is equally significant to adequately prepare for a PAT test to ensure compliance and safety of electrical appliances. Preparation begins with a comprehensive pre-test checklist encompassing all equipment and tools required.
Equipment preparation is critical; ensure all devices are accessible, properly labelled, and free from obvious defects. Technician requirements must also be addressed. Verify that technicians have the necessary qualifications and are familiar with the latest safety standards and testing procedures.
Proper appointment scheduling is essential to avoid business disruptions and allocate sufficient time for each test. Organise the workspace to ensure a clean and safe environment for testing, which will facilitate easy movement and reduce the risk of accidents.
Communication protocols between the technician and client are paramount for a smooth process. Discuss the scope of testing, address any specific concerns, and outline the expected duration. Before testing, a thorough risk assessment should be conducted to identify potential hazards associated with electrical testing in the specific environment.
Documentation procedures should be clear and adhered to meticulously. This includes recording the results of each test, any faults found, and actions taken. Setting client expectations before testing begins will help manage their anticipation of the process and results.
PAT Testing Certification Explained
PAT Testing Certification serves as a critical validation, verifying that electrical appliances meet the necessary safety standards for operational use in commercial environments. This certification process is not just a formality but a rigorous assessment that ensures the safety and efficiency of electrical equipment, protecting both property and people from potential hazards. The process involves several meticulous steps to achieve certification guided by established testing standards and certification requirements. Accredited organisations recognised for their expertise in electrical safety conduct these tests. Their assessors are trained through specialised training courses that equip them with the necessary skills to evaluate various electrical appliances against the current safety norms.
Documentation Process
Detailed records of each appliance’s condition, test results, and any repairs or adjustments made.
Equipment Labeling
After testing, each appliance is labelled with a pass or fail tag, along with the inspection date and the inspector’s identification.
Certification Validity and Renewal Procedures
Certificates are issued with a validity period, after which re-certification is necessary to ensure ongoing compliance.
Further aspects integral to maintaining the certification’s credibility include regular inspection intervals, compliance audits conducted by third-party auditors, and strict adherence to renewal procedures. This systematic approach ensures that all certified appliances continue to operate safely until the next evaluation, thus supporting uninterrupted business operations and reinforcing safety in the workplace.
What tests are done for PAT testing?
During a PAT (Portable Appliance Testing) session, several specific tests are conducted to determine the safety and functionality of electrical appliances. These tests ensure that all portable devices meet rigorous safety standards and perform reliably under varied conditions. Each test targets different aspects of electrical safety and functionality.
The initial step in PAT testing is a thorough visual inspection. This involves examining the appliance, its plug, and the cable for any signs of damage or wear. Technicians look for frayed cords, damaged plugs, and other visible defects that might compromise safety.
Following the visual assessment, more detailed and technical evaluations are conducted, including:
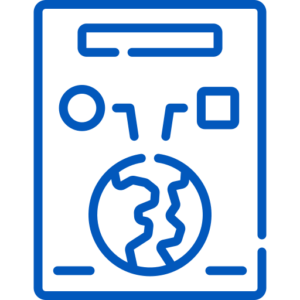
Earth Continuity
Test
Essential for Class I appliances, this test ensures a continuous path between the earth pin on the plug and the appliance’s case, which is crucial for user safety in case of a fault.
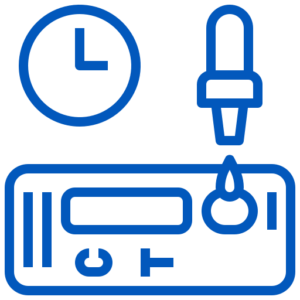
Insulation Resistance Test
This test checks the effectiveness of the electrical insulation between the current-carrying parts and any exposed metal parts. Healthy insulation levels prevent accidental shocks and are integral to operational safety.
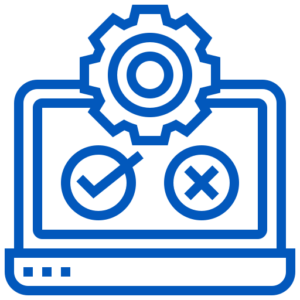
Functional
Testing
Beyond safety, confirming that the appliance performs its intended function correctly is vital. This test simulates standard operational conditions to ensure the device works as expected.
Book NowAdditional tests may include leakage current testing and polarity checks, which further ensure the device’s compliance with safety standards. Technicians can use advanced testing equipment to assess the risk and accurately classify the appliance. Each test is pivotal in the comprehensive risk assessment process, underscoring the commitment to maintaining high safety standards in electrical appliance usage.
Why is PAT Testing Essential for Businesses in London?
Portable Appliance Testing (PAT) is a critical procedure for businesses across London, ensuring that all electrical equipment is safe and functional. This process not only complies with the UK’s stringent health and safety regulations but also mitigates the risk of electrical accidents, which can lead to serious injuries or even fatalities. For businesses, the implications of neglecting this responsibility are far-reaching, encompassing legal, financial, and reputational risks. Therefore, maintaining regular PAT testing is not just a regulatory formality but a fundamental aspect of operational integrity and workplace safety.
London Safety Certificate serves North London, focusing on providing top-tier emergency PAT testing services, ensuring that businesses do not compromise on safety or quality. The service thoroughly inspects all portable electrical appliances using specialised testing equipment to detect potential safety defects. The importance of such testing cannot be overstated, as it helps businesses prevent electrical hazards that could lead to costly downtime or, worse, endanger lives. By adhering to the latest safety standards, businesses can ensure a safer working environment and demonstrate their commitment to employee well-being and customer safety.
PAT testing with the London Safety Certificate involves a detailed examination and testing of every appliance to assess its safety and compliance with current electrical standards. A detailed report is provided post-assessment, outlining the condition of the equipment and any necessary recommendations or actions. This proactive approach helps businesses in North London maintain compliance with safety regulations. It enhances the longevity of their electrical equipment, optimising operational efficiency and minimising the risk of unexpected equipment failures that could disrupt business operations.
FAQs
In London, regulations dictate the validity period of a PAT testing certificate. Adherence requires understanding renewal frequency, testing accuracy, provider accreditation, and customised reporting. For safety and legal compliance, maintain compliance with these rules.
To maintain the validity and accuracy of your PAT testing certification over time, prioritise regular maintenance, adhere to inspection intervals, fulfil training requirements, maintain detailed record keeping, and conduct thorough risk assessments. Consistency is key for compliance and safety.
Would you be able to find a trusted PAT testing provider in London? Start by conducting an accreditation check. It’s crucial for consumer trust, service quality, and credibility assurance. Could you verify their credentials thoroughly for peace of mind?
Consider industry standards, certification criteria, and thorough testing when differentiating PAT testing certificates. Verify credibility with recognised qualifications and adherence to regulations. Confirm the certificate meets industry requirements for thorough and reliable testing.
You can request customised reporting and additional documentation to meet internal or industry standards. Different certifications may offer varying levels of detail. Verify your PAT testing certificate aligns with your needs for compliance and safety.